3D printing has been slowly but surely ramping up as a viable construction technology, with communities of 3D printed homes being built in California, Virginia, Texas, and Mexico, among others. Now a new development on the other side of the Atlantic is joining this list.
Last week 14Trees, a joint venture between Swiss sustainable construction company Holcim and British International Investment, announced completion of the first 10 units of a 3D printed housing project in Kilifi, Kenya. The community is called Mvule Gardens, and it will eventually consist of 52 single-family homes.
The first homes to be completed include six three-bedroom houses that are 836 square feet each and four two-bedrooms measuring 616 square feet. Printing started in October 2022, with the goal of putting up the walls of one house each week for 10 weeks. According to Holcim, printing the walls of the two-bedroom homes took just 18 hours.
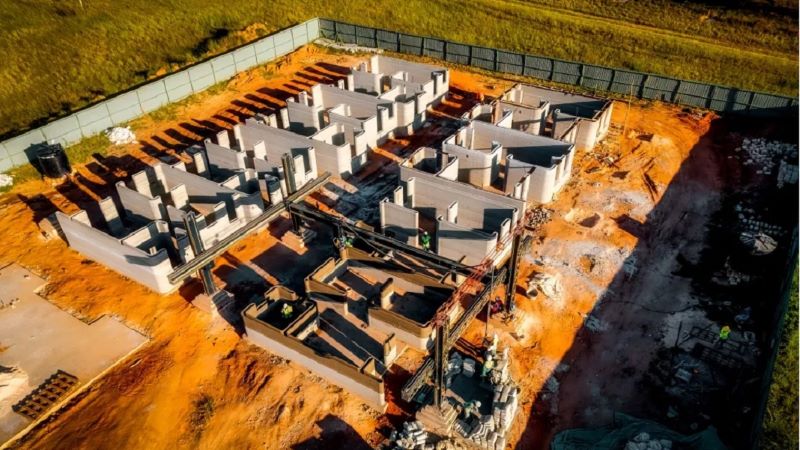
The printer being used for the project is a BOD2 from Danish company COBOD. The company says the BOD2 is the fastest 3D construction printer on the market, laying down one meter’s worth of material per second. The gantry-style printer moves between three axes on a metal frame, and requires two human operators to run it. The BOD2 was used in 2020 to print an apartment building in Germany, and in 2021 for a school in Malawi.
Kilifi is in south-east Kenya, on the coast about 35 miles northeast of Mombasa. Prices for the two-bedroom houses at Mvule Gardens start at 3,610,000 Kenyan shillings, about $28,620. While this would be quite affordable for the average American, it’s less so for the average Kenyan.
However, 14Trees says one of its main goals is to continue lowering construction costs with each phase of the project, ultimately offering homes for 20 percent less than standard houses. They’re also planning to let future homeowners design their own floor plans, taking advantage of the customizable and modular nature of 3D printing construction.
The project has already received an EDGE Advanced sustainable design certification from the IFC, the World Bank’s development finance institution, which recognizes resource-efficient buildings with the potential to be zero-carbon.
As you’ve probably heard, or perhaps experienced first-hand, there’s a massive housing shortage not just in the US, but all over the world, with millions more people in need of homes than there are homes available. The best way to solve this crisis is to build, but we have to do so in a way that’s smart, sustainable, and affordable—not to mention fast. According to 14Trees, there’s a deficit of nearly two million homes in Kenya alone.
There’s some debate about whether 3D printing is truly a viable and scalable solution to the housing shortage. Critics point out that the cost savings likely won’t be as significant as all the hype implies, nor will the eco-friendliness, since the homes use cement and cement is a major source of carbon emissions. Also, 3D printing is most practical for single-family homes, and less applicable for the dense, multi-story housing that will go furthest in closing the supply gap.
Will 3D printed homes really become the “Teslas of housing”? That remains to be seen, but as companies and governments work towards solving the housing crisis in the US and across the world, 3D printed communities are better than the alternative, which in many cases is nothing.
The first 10 Mvule Gardens homes are now being roofed and painted, and will be turned over to their new owners upon completion as the next 10 homes get underway.
Image Credit: Holcim
* This article was originally published at Singularity Hub
0 Comments