We’re surrounded by ingenious substances: a menu of metal alloys that can wrap up leftovers or skin rockets, paints in any color imaginable, and ever-morphing digital displays. Virtually all of these exploit the natural properties of the underlying materials.
But an emerging class of materials is more versatile, even programmable.
Known as metamaterials, these substances are meticulously engineered such that their structural makeup—as opposed to their composition—determines their properties. Some metamaterials might make long-distance wireless power transfer practical, others could bring “invisibility cloaks” or futuristic materials that respond to brainwaves.
But most examples are solid metamaterials—a Harvard team wondered if they could make a metafluid. As it turns out, yes, absolutely. The team recently described their results in Nature.
“Unlike solid metamaterials, metafluids have the unique ability to flow and adapt to the shape of their container,” Katia Bertoldi, a professor in applied mechanics at Harvard and senior author of the paper, said in a press release. “Our goal was to create a metafluid that not only possesses these remarkable attributes but also provides a platform for programmable viscosity, compressibility, and optical properties.”
The team’s metafluid is made up of hundreds of thousands of tiny, stretchy spheres—each between 50 to 500 microns across—suspended in oil. The spheres change shape depending on the pressure of the surrounding oil. At higher pressures, they deform, one hemisphere collapsing inward into a kind of half moon shape. They then resume their original spherical shape when the pressure is relieved.
The metafluid’s properties—such as viscosity or opacity—change depending on which of these shapes its constituent spheres assume. The fluid’s properties can be fine-tuned based on how many spheres are in the liquid and how big or thick they are.
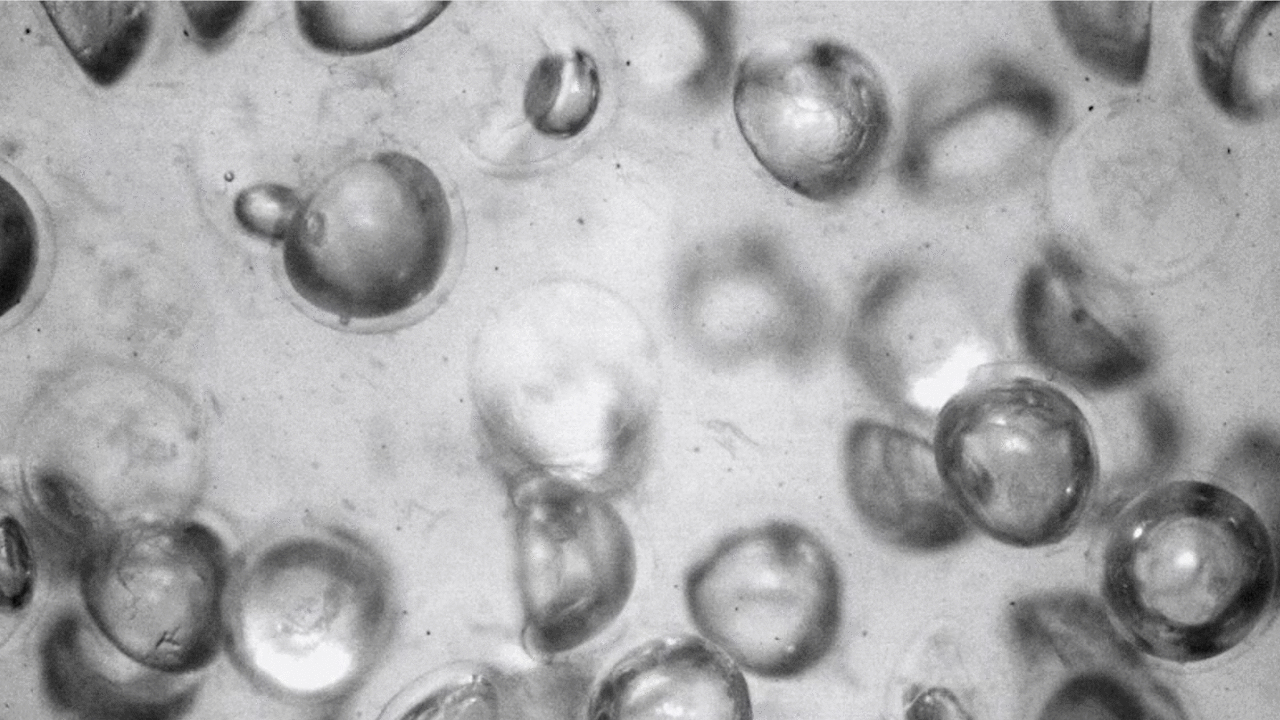
As a proof of concept, the team filled a hydraulic robotic gripper with their metafluid. Robots usually have to be programmed to sense objects and adjust grip strength. The team showed the gripper could automatically adapt to a blueberry, a glass, and an egg without additional sensing or programming required. The pressure of each object “programmed” the liquid to adjust, allowing the gripper to pick up all three, undamaged, with ease.
The team also showed the metafluid could switch from opaque, when its constituents were spherical, to more transparent, when they collapsed. The latter shape, the researchers said, functions like a lens focusing light, while the former scatters light.
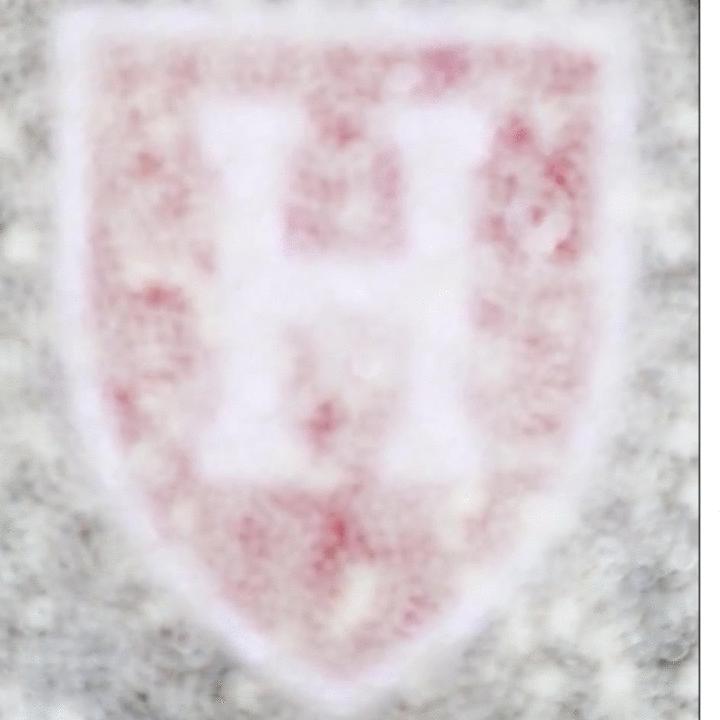
Also of note, the metafluid behaves like a Newtonian fluid when its components are spherical, meaning its viscosity only changes with shifts in temperature. When they collapse, however, it becomes a non-Newtonian fluid, where its viscosity changes depending on the shear forces present. The greater the shear force—that is, parallel forces pushing in opposite directions—the more liquid the metafluid becomes.
Next, the team will investigate additional properties—such as how their creation’s acoustics and thermodynamics change with pressure—and look into commercialization. Making the elastic spheres themselves is fairly straightforward, and they think metafluids like theirs might be useful in robots, as “intelligent” shock absorbers, or in color-changing e-inks.
“The application space for these scalable, easy-to-produce metafluids is huge,” said Bertoldi.
Of course, the team’s creation is still in the research phase. There are a plenty of hoops yet to navigate before it shows up in products we all might enjoy. Still, the work adds to a growing list of metamaterials—and shows the promise of going from solid to liquid.
Image Credit: Adel Djellouli/Harvard SEAS
* This article was originally published at Singularity Hub
0 Comments